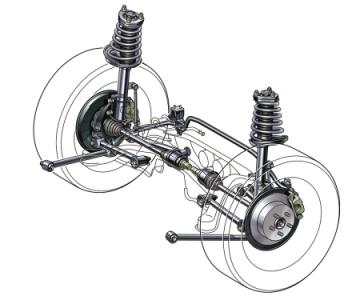
隨著社會經濟的發展,汽車市場的產能需求也越來越大,同時人們對汽車的性能要求越來越高,這就要求各個汽車生產商在不斷提高產能的同時,也要提升汽車及其零部件的性能。懸架系統作為汽車底盤的關鍵部分,對汽車的行駛安全可靠性和實用性能都有重要的影響,也是現在汽車設計研究的熱點。在實際使用中,扭力梁式后懸架的破壞多數是由于強度失效引起的。本文采用有限元方法對扭力梁式后懸架進行強度分析并根據計算結果對懸架進行相應的結構優化,優化結果表明優化后的結構可以有效地降低結構的應力,增加后懸架強度,避免扭力梁式后懸架在轉向和極限扭轉工況下的破壞。該方案對扭力梁式后懸架的研發具有一定的參考借鑒作用。
本文對扭力梁式后懸架進行極限左轉向、沖擊、制動、極限扭轉4個工況的強度分析。在建立模型之前,首先對扭力梁式后懸架的4種工況進行受力分析。結合轉向加速度產生的側傾效應,后輪輪心載荷按如下方法計算,以上3種工況的計算公式中:m為整車滿載質量,1690kg;a為轉向或制動加速度,轉向和制動時a=0.8,其中g=9.8N,沖擊時取a=2.5g;h為整車滿載質心高度,504mm;L為后輪距,1520mm(空);n為軸距,2700r/min(空);P偽后軸滿載荷載,787kg;P整車滿載荷;R為輪胎半徑,316mm。本文根據企業提供的極限扭轉試驗工況進行模擬,在兩端懸架制動安裝板Z向分別添加70N/mm和-70N/mm的強制位移,模擬扭力梁式后懸架在極限扭轉下的工況。
為了在減少計算量的同時又能充分反映原模型的實際情況,本文對結構中橡膠襯套及穩定桿等連接單元分別采用單點彈簧和彈簧等進行了模擬。本文采用單點彈簧等效替代橡膠襯套,經多次試驗驗證,單點彈簧可以兼顧橡膠襯套在軸向和徑向上的不同剛度。使用單點彈簧模擬橡膠襯套時,根據橡膠襯套特點在一側襯套座建立3個單點彈簧,模擬橡膠襯套的3個方向的剛度。單點彈簧3個自由度剛度數值見表1。用同樣的方法在懸架另一將扭力梁式后懸架幾何模型導入有限元前處理軟件Hypermesh中建立有限元模型。該扭力梁式后懸架所用材料為QSTE420TM冷成型熱軋汽車結構鋼板,前處理軟件Hypermesh中建立的扭力梁式后懸架的有限元模型,模型的單元目標尺寸為5mm,單元總數為33602,節點數為34520,三角形網格個數為928,其余為四邊形網格,其中在焊縫處為了更形象地描述焊點,采用的是六節點的實體網格進行模擬。在懸架彈簧底座、襯套、制動安裝地板各自的中心處建立獨立節點,并以該節點為中心建立RBE2剛性單元,在懸架彈簧底座處建立3個彈簧單元。根據實際使用工況要求,設定彈簧長度為206mm,剛度為27.3N/mm。
本文中使用單點彈簧模擬橡膠襯套,4種工況在兩端襯套處均約束相應自由度。其他邊界條件如下:D左轉向工況。約束:約束兩端彈簧頂端所有自由度。載荷:在制動安裝底板板中心施加轉矩M內、M外,轉向力F內、F外以及支撐力F;2)沖擊工況。載荷:在沖擊工況時,由于沖擊加速度較大,此時后懸架的彈簧已經被壓縮到極限位置,阻尼器將起作用,因此通過強制位移將后輪中心上擺至極限位置作為位移約束,我們在后懸架彈簧安裝位置分別施加大小為5201N的力,并在制動安裝底板中心施加沖擊力;3)制動工況。約束:兩端彈簧頂端所有自由度。載荷:在兩端安裝底板中心分別施加X方向的制動力、制動力矩和Z方向的支撐力。4)極限扭轉工況。約束:約束兩端彈簧頂端所有自由度。載荷:根據極限扭轉工況分析,在懸架兩端制動安裝底板中心Z方向分別施加70mm和-70mm的強制位移。根據應力云圖顯示得知:制動工況最大應力出現在彈簧底座,應力值為204MPa,沖擊工況最大應力出現在彈簧底座與后懸架橫梁連接處,應力值為289MPa,彈簧安裝支座材料為SAPH440,屈服強度為305MPa;兩種工況應力低于材料的屈服強度,在后懸架實際工況中不會發生破壞。在左轉向工況中,后懸架橫梁內加強板處以及后懸架梁端應力值較大,最大應力值483MPa。極限扭轉工況中,最大應力出現在梁端,不符合實際使用情況,最大應力值為515MPa,該橫梁采用材料為QSTE420TM冷成型熱軋汽車結構鋼板,材料屈服極限為420MPa,左轉向和極限扭轉工況最大應力值均大于材料的屈服極限420MPa,扭力梁式后懸架會因應力較大而導致斷裂,需要改進后懸架結構,減少應力值,增加后懸架強度。
專業從事機械產品設計│有限元分析│強度分析│結構優化│技術服務與解決方案
杭州那泰科技有限公司
本文出自杭州那泰科技有限公司www.yw15777.cn,轉載請注明出處和相關鏈接!