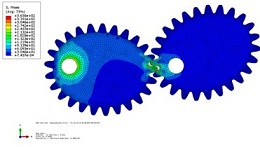
發動機將內嚙合齒輪應用于膨脹機。但目前對內嚙合轉子膨脹機的結構設計和工作特性研究上比較薄弱,從膨脹機的失效情況來看,內嚙合齒輪是最容易出故障的零件之一,因而有必要對齒輪工作接觸狀態下的強度性能進行合理的評估。利用有限元分析軟件ANSYS,對內嚙合齒輪建立比較精確的分析模型,準確掌握齒輪接觸應力分布特點,得到的研究結果對內嚙合轉子膨脹機中齒輪的設計和提高設計效率具有重要意義。
內嚙合轉子膨脹機齒輪設計參考齒輪式油泵相關型線的設計過程與方法,采用完整的連續封閉的短幅外擺線的等距曲線作為內轉子齒廓,外轉子采用與其共扼的均布圓弧作為齒形。經實驗討論擬用基本參數如表。經計算得到其幾何尺寸參數如表,利用Pro/E軟件建立齒輪的幾何模型,將建好的2個齒輪進行裝配。裝配好的齒輪模型如圖,所示因為該膨脹機的最高溫度可達到600℃以上,所以選擇耐高溫的材料。本文選擇是高溫合金GH4169,彈性模量206GPa,泊松比為0.30,將齒輪在Pro/E模型轉化為ICES格式導入到ANSYS中,將齒輪劃分為三個部分:接觸區域、接觸相鄰區域、非接觸區域,對接觸區域和接觸相鄰區域適當的加密。選擇smartsize智能網格劃分,6級精度,單擊mesh,選擇所要劃分的兩個齒輪。然后在齒輪嚙合處進行局部加密,得出最終劃分出來的自由網格模型為如圖。用TARGE169和CONTA171或CONTAN172定義2D接觸對。用TARGE170和CONTAN173或CONTAN174定義3D接觸對。
將內齒輪外廓邊界上的節點X,Y,Z方向的位移設置為零,即約束內齒輪的徑向自由度、外齒輪的徑向和轉向自由度。由于采用接觸模型計算,載荷可以直接施加到內齒輪。將嚙合內齒輪的齒廓線2和外齒輪的齒廓線1設置為接觸對:齒廓線1為接觸面,齒廓線2為目標面。將其接觸剛度因子FKN和拉格朗日算法允許的最大滲透量FTLON分別設置為1.0和0.1。接觸對設置見圖。在內嚙合齒輪膨脹機中,主動輪內轉子通過軸輸入轉矩傳遞給外轉子。對外轉子和內轉子的內圓面施加位移約束,約束X軸,再約束外齒輪安裝孔表面上所有節點的自由度;同時在內轉子內圓面施加轉矩,輸入五的值為243N(以發動機功率100kW計算得出)。在實際工作狀況中,需要考慮轉子膨脹機在齒輪嚙合情況下,7個工作腔內的氣體對內外轉子產生接觸應力的影響。由于若考慮氣體壓力,對計算機的硬件要求過高,且求解繁瑣,耗時過長,所以不予考慮。
在內外齒輪嚙合的情況下,對內轉子施加243N的扭矩,使其繞中心軸進行順時針轉動。由靜應力分析圖可得知:最大應力在接觸面1上,該處的齒輪最大應力主要集中在外齒輪齒頂處與內齒輪齒根處,達到了946.582MPa,并逐漸向周圍擴散減小。接觸面2上齒輪的應力相比于接觸面1已經大幅減小,最大應力值降低為631.002MPa。接觸面3處內齒輪齒根處受力為210.352MPa左右,已大幅度下降。接觸面4內外齒輪嚙合處應力都發生在齒頂處,集中在一個極小范圍內為105.176MPa。接觸面5、接觸面6、接觸面7處幾乎不受力。
通過應力云圖可以看出齒輪在接觸點和齒根處應力集中,最容易發生破壞。由圖比較可知,在內嚙合轉子膨脹機工作情況下,接觸面1受到的壓力最大,也最容易發生斷裂,尤其在內轉子的齒根圓角處。這是因為主動輪為內轉子,內轉子帶動外轉子時,接觸面1處于完全嚙合情況下,傳動效率最大,所以在此處產生的接觸應力最大。同時接觸面1也處于工作腔滿載荷情況下,此時壓力達到最大,理論值約為6atm,接觸面1不僅受到內外轉子完全嚙合產生的接觸應力,同時還受到了高壓氣體對齒輪產生的壓力,此處最容易折斷,這是膨脹機工作情況下最容易發生故障的原因之一,其余6個接觸面的接觸力逐漸減小18]0本實驗采用了高溫合金GH4169,該材料在高溫時有較大屈服強度,符合實驗要求。為了減小內轉子的齒根處的應力,可以對齒輪結構設計時改變其參數,加工時進行熱處理和加大局部工藝強度等。
1)在高速工作情況下的膨脹機每個接觸面都在不斷交替承受著較大的作用力,所以在材料選擇方面,需要選用高強度的材料,本文采用高溫合金GH4169符合實驗要求,傳統的45號鋼很難達到強度要求。2)內嚙合齒輪式膨脹機內轉子的最大應力發生在齒根的圓角處。在齒輪嚙合過程中,此處最容易折斷,這是膨脹機工作情況下易發生故障的原因之一。3)根據以上的數據分析,對內嚙合齒輪膨脹機的齒輪結構的設計、參數的優化和強度的校核方面提供一定的參考價值。
專業從事機械產品設計│有限元分析│強度分析│結構優化│技術服務與解決方案
杭州那泰科技有限公司
本文出自杭州那泰科技有限公司www.yw15777.cn,轉載請注明出處和相關鏈接!